Information
The Role Of Root Cause Failure Analysis In Risk Mitigation And Compliance

In our increasingly complex and interconnected business environment, companies face a myriad of dangers that could affect their business operations as well as their bottom line. Recognizing the causes behind errors is vital for risk reduction and to ensure compliance with the rules and regulations.
Root cause failure analysis (RCFA) is an extremely effective method to help organizations discover the root causes of failure and enables them to take preventive maintenance and measures to avoid recurring failures.
This article focuses on the crucial significance of RCFA for risk mitigation and the observance of.
Table of Contents
What & Why ‘Root Cause Failure Analysis’?
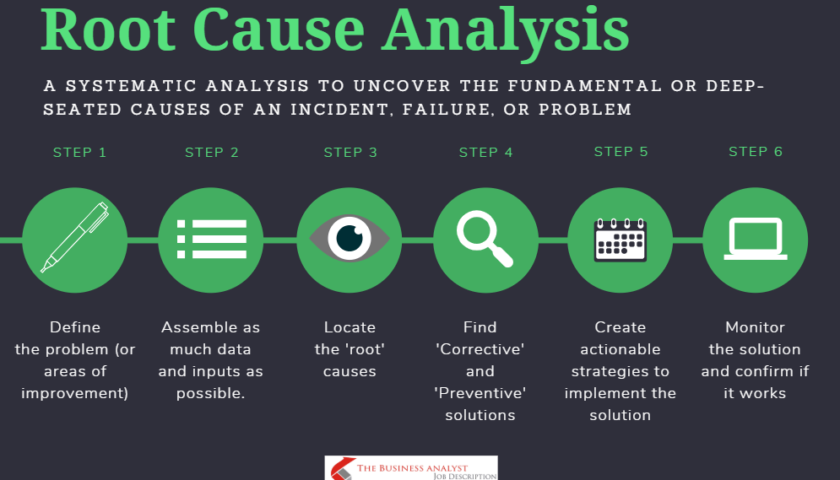
Root cause failure analysis is the procedure to determine the cause of malfunctioning equipment, process issue or quality issue, safety incident, environmental issue, or other issues within a facility.
RCFA provides an organizational structure with a well-defined approach and strategies to prevent or reduce the causes of failure that ultimately hurt those who are affected, harm the property or equipment, cause the loss of production, or bring with negative impacts to the natural environment.
4 Benefits Of Root Cause Failure Analysis

Avoiding Recurrences & Cost Reduction
Avoiding recurrences and cost reduction by discovering the causes of failure, RCFA enables organizations to take corrective measures to address the root causes, thus preventing repeat failures of the same nature from occurring. Root cause failure analysis can help reduce the costs that are associated with failures by making sure to address the root issues, making it unnecessary to make recurring solutions.
Maintaining Your Competitive Edge
In the current highly competitive world of manufacturing, it is vital to make use of resources as effectively and efficiently as you can. That is especially true for tasks at the workplace like problem-solving.
We will discover that RCA is the ideal and perhaps the only option to identify and fix long-term issues that are recurring. It is one of the most effective methods for manufacturers to use as well as one of the reasons they choose to use this method.
Improvement In Decision Making
RCFA offers valuable insight into the weak points and weaknesses within the processes of an organization, which allows an informed and targeted decision-making process for risk reduction and the allocation of resources.
Increased Safety and Compliance Understanding the root cause of RCFA assists organizations in ensuring conformity with industry regulations and standards. This results in improved security and a reduction in regulatory and legal risks. Also, it is best in planning and scheduling work to improve the business management.
Easy To Use & High-Quality Effectiveness
High-quality effectiveness and efficiency can be gained by companies that focus on the root cause rather than those who address the symptoms. However, there are a variety of advantages of the root cause analysis process that could be spotted.
One of them is that it’s rational and easy to master, and is easy to apply. Furthermore, since RCA is based on fact and data rather than theories or assumptions, in order to work it improves the effectiveness of its solutions, as do the contributions of all of the team participants.
There are additional benefits that can be derived from creating RCA, an everyday routine that individuals are able to say, “This is the way we problem-solve”. It is the most significant benefit that RCA will transform an existing reactive culture into one that is active problem-solvers. This, in turn, minimizes variation in the processes and counteracts a risk-aversion attitude.
Steps In Root Cause Failure Analysis
1. Data Collection
It’s important to collect data from every process of your company. Collect every piece of information pertinent to the event that caused the failure, such as incidents reports, Maintenance records, incident reports, as well as witnesses’ statements.
2. Timeline Reconstruction
Making an event timeline that traces the incidents leading to failing to pinpoint events that could trigger the failure and their contributing elements is helpful especially in situations where you can’t easily pinpoint.
3. Analytical Techniques
Using various instruments and techniques like diagrams showing cause and effect reasons and fault tree analysis as well as failure mode and effect analysis (FMEA) to help determine the root cause of a problem is helpful. The root cause identification process involves thorough examination and elimination; you can identify the main factors contributing to the malfunction. It’s important to have a corrective action plan for addressing the root causes identified and implementing the necessary changes, and evaluating their efficacy.
4. Documentation And Reporting
What’s important with RCFA is documentation. Documenting the results and steps taken and sharing results with the relevant parties as well as ensuring that the proper documentation is in place can be used for future reference. Companies can just go back to these documents if they encounter something similar.
Challenges And Considerations
- Access to complete and accurate data is vital to the success of RCFA. The organization should have a robust system for managing and collecting data.
- Performing RCFA requires skilled staff who are knowledgeable about investigative methods as well as analysis instruments. A sufficient number of resources should be provided for a thorough analysis.
- Organizational culture is an environment that promotes the sharing of information and learning from mistakes is crucial for a successful RCFA. Companies should provide the environment to encourage accountability and transparency.
- Continuous improvement with RCFA is a continuous method that must be constantly enhanced based on the lessons learned. A regular review and analysis of past failures may aid in improving the method.
RCFA Varieties
RCFA is available in various designs based on the challenge you’re trying to solve. The following is a look at RCFA:
- Safety-based RCA: is a part of the field of occupational health and safety and the study of accidents. This form of analysis of the root causes is utilized to identify the reason why the accident occurred in the workplace. i.e., why someone was injured, or an item fell off by accident (a worker working from a high height).
- Production-based RCA: is utilized for manufacturing in order to control quality. This can help you determine the reason why injection-molded plastic parts have come from the production line with a warped appearance.
- Process-based RCA: is utilized in both business manufacturing and in the production process to identify the source of failure in a process or system. It can be applied to accounting to find out the reason why vendors don’t get payment promptly.
- Failure-based RCA: is utilized for maintenance management and engineering to find the root reason for any kind of device failure.
- Systems-based RCA: was developed as a blend with some of the analysis methods for root causes mentioned above. The method is one that blends several methods of RCA. It is applicable to numerous fields or applications.
Bottom Line
Root cause failure analysis plays a crucial role in reducing risk and ensuring the compliance of organizations. In locating the underlying cause of problems, RCFA helps businesses implement specific corrective measures, improve the safety of their employees, decrease costs, and ensure that they are in compliance with laws.
By taking on RCFA as a proactive strategy, companies can limit failures and incidents or risks as well as create a durable and dependable operating framework.
To know more about keep reading Lemony Blog.

-
Business3 years ago
How to Do Long-Distance Moves with Children
-
Travel2 years ago
Quick Guide: Moving To Santa Rosa?
-
Real Estate3 years ago
Why Dubai Festival City is a Great Neighbourhood for Young Learners
-
Business3 years ago
Is Guest Posting a Good Inbound Marketing Strategy?
-
Business1 year ago
The Ultimate Guide To Thriving In Your Printing Franchise
-
Business1 year ago
Exploring The Benefits And Challenges Of Restaurant Franchising
-
Tech3 years ago
Cyber Table That Will Change Your Life
-
Lifestyle1 year ago
Dallas’ Hidden Gems: 6 Must-Try Restaurants Off The Beaten Path!
Recent Comments