Business
Understanding The Impact Of Plates And Gaskets On Industrial Operations
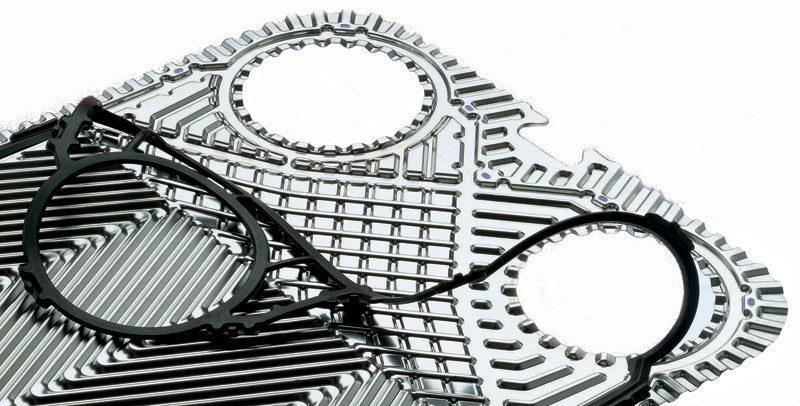
Table of Contents
Key Takeaways:
- Plates and gaskets are vital for maintaining the efficiency and safety of industrial systems.
- Material choice significantly affects the durability and suitability of these components under various operational conditions.
- Technological advancements enhance the performance and sustainability of plates and gaskets.
- Underestimating the role of proper installation can lead to system failures despite the components’ quality.
Introduction To Industrial Components
Complex industrial systems are akin to a well-orchestrated symphony, where each instrument is vital to the harmony of the whole. The plates and gaskets are hidden within this harmony, perhaps lacking visual grandeur but critical to the system’s efficiency and integrity. For professionals and decision-makers seeking heat exchanger parts for sale, it is crucial to comprehend the nuances of these components. Understanding their functionality serves to not only ensure system performance but also inform smart procurement decisions that have widespread implications on operational costs and reliability.
Diving Into Plate Heat Exchangers
The unassuming plate heat exchanger is crucial in efficiently handling thermal energy. Its development represented a notable leap forward in transferring heat among multiple fluids. Crafted from thin metal plates, which optimize surface area while minimizing bulk, these heat exchangers excel in effectiveness. Explore available heat exchanger parts for sale to ensure smooth operation. By employing a counter-flow arrangement, they facilitate a remarkable transfer of heat, which is vital for power plants, food and beverage production, and even aboard ships. The genius of this system is the enhanced control it provides over temperature modulation, essential for the precision required in delicate industrial operations.
The Anatomy Of A Gasket
When dissecting the anatomy of a gasket, one discovers an element fashioned for resilience. These indispensable seals are fabricated from various materials, from rubber, which affords flexibility, to graphite, known for its resistance to high temperatures. Gaskets fill the space between mating surfaces, contoured precisely to prevent the leakage of liquids or gases. They accommodate the microscopic irregularities, ensuring a complete seal under a broad spectrum of conditions. This sealing capability is foundational to the safe operation of countless industrial applications, from pipelines transporting hazardous chemicals to engines driving the mechanisms of powerful machines.
Synergy Between Plates And Gaskets
The collaboration between plates and gaskets illustrates industrial symbiosis. Gaskets, with their supple nature, mold to the contours of the plates to create a secure seal, ensuring that fluids within a heat exchanger travel their intended paths without Commingle. This synergy is paramount in preserving the heat transfer process’s efficiency and safeguarding against the perils of cross-contamination. When these components function correctly in unison, they significantly reduce the risk of operational failures, safeguarding assets and protecting the workforce’s wellbeing.
Importance Of Material Choice In Plates And Gaskets
Selecting the correct materials for plates and gaskets transcends simple preference—it is a necessary decision that directly impacts the longevity and performance of industrial systems. The right choice depends on thoroughly understanding operational environments, including corrosive substances, variable temperature ranges, and exposure to extreme pressures. Such conditions necessitate materials that endure without degradation, maintaining their original properties over time. For example, selecting a gasket material incompatible with the fluid it contacts could result in leaks, equipment failure, or, worst cases, catastrophic accidents. Therefore, the material selection process is a proactive step toward securing operation integrity and worker safety.
Lifespan And Maintenance: Keeping Systems Operational
When maintaining industrial components, “a stitch in time saves nine” is entirely appropriate. Proactive inspection and maintenance are linchpins for enduring the performance of plates and gaskets. Components should be monitored for signs of wear, such as deformation, hardening, or corrosion. Anticipating the need for replacements can mitigate downtime, with the added benefit of a more predictable maintenance budget. By establishing and adhering to a regular maintenance schedule, facility managers can extend the lifespan of their equipment, ensuring it remains a reliable pillar in the industrial processes that keep the wheels of industry turning steadfastly.
Advances In Plate And Gasket Technology
Through the relentless pursuit of innovation, today’s plates and gaskets surpass those of yesteryears in durability and adaptability. By harnessing the findings from research on advanced gasket materials, manufacturers have expanded the capabilities of these components to cater to ever-evolving industrial demands. Materials engineered with enhanced resilience to chemical attacks, thermal extremes, and mechanical stresses pave the way for plates and gaskets that perform better and have less environmental impact due to their increased lifespan and efficiency.
Environmental Impacts And Energy Efficiency
Our industrial endeavors have a significant bearing on the health of our planet. As such, the role of energy efficiency and minimal environmental impact must be addressed. A properly sealed system with energy-efficient plates and gaskets utilizes less fuel and generates fewer emissions. This conscious pursuit of better sealing technology reflects a broader commitment to sustainable practices within the industry, a shift that aims to secure a cleaner, greener future. In this way, seemingly insignificant components like plates and gaskets become critical players in the effort to preserve our environment for generations to come.
Selection And Installation Best Practices
Selecting the ideal plates and gaskets involves a sophisticated understanding of the systems they will serve. Decisions must balance the mechanical demands with chemical compatibility and thermal dynamics. Then comes the critical installation process—a task that, if performed improperly, can lead to premature failure and costly repairs. The craftsmanship in installing these components is just as important as the quality of the materials chosen. Mastery of installation techniques helps to ensure that plates and gaskets perform to their fullest potential, providing secure, leak-proof joining critical to the operation of various industrial systems.
Case Studies: Real-world Applications And Benefits
One only needs to look at the success stories emerging from diverse industrial landscapes to see the value of high-quality plates and gaskets. These testimonials paint a vivid picture, from the performance gains in heat exchangers following the adoption of cutting-edge gasket designs to the enhanced operational efficiency observed in modern manufacturing facilities. Innovations such as those highlighted by recent developments in heat pump technology further affirm the significant role of plates and gaskets. They underscore the tangible improvements the right components can make, emphasizing their vital position in our quest for industrial advancement and ecological responsibility.

-
Business3 years ago
How to Do Long-Distance Moves with Children
-
Travel2 years ago
Quick Guide: Moving To Santa Rosa?
-
Real Estate3 years ago
Why Dubai Festival City is a Great Neighbourhood for Young Learners
-
Business3 years ago
Is Guest Posting a Good Inbound Marketing Strategy?
-
Business1 year ago
The Ultimate Guide To Thriving In Your Printing Franchise
-
Business1 year ago
Exploring The Benefits And Challenges Of Restaurant Franchising
-
Tech3 years ago
Cyber Table That Will Change Your Life
-
Lifestyle1 year ago
Dallas’ Hidden Gems: 6 Must-Try Restaurants Off The Beaten Path!
Recent Comments