Business
Importance of Material Handling Equipment and the Different Types

The material handling industry focuses on the movement, protection, control, and storage of materials and items for the many industries that need them, such as the warehousing, distribution, manufacturing, disposal, and consumption industries. It’s one of the crucial steps in supply chain management, and it includes a few different types of equipment and applications that can be either manual, semi-automatic and automatic.
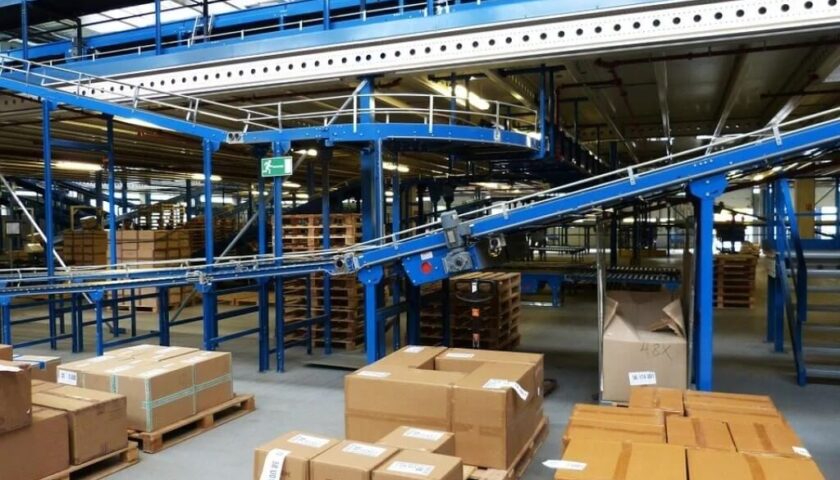
Table of Contents
Manual Material Handling
Manual material handling equipment implies that there is some manual labor included in the movement of the materials and products, such as lifting, carrying, filling, and emptying. Manual material handling equipment is more affordable, but it still poses workplace safety risks, most notably, musculoskeletal disorders. Trolleys are arguably the most popular piece of manual material handling equipment. There are many different types of trolleys suitable for a variety of applications. You can buy a trolley online, in hardware or specialized material handling equipment stores. Australian standard pallets, designed to meet the rigorous specifications for size, strength, and durability, play a crucial role in efficient and standardized logistics across various industries in the country.
Standing all day, especially on hard surfaces like concrete, can lead to fatigue for workers. Foot muscles, as well as those in the legs, back, and other parts of the body, tire easily, and the problem can be exacerbated when employees don’t wear appropriate footwear. So one must invest in safety shoes for their employees
Semi-Automatic and Automatic Material Handling
Semi-automatic and automatic material handling equipment reduces the amount of manual labor included in the movement of materials and products. Most equipment falls into the category of semi-automatic, simply because workers still have to load and unload the materials or products and drive the equipment. This is the case due to the fact that full-out automation is too expensive for most facilities.
The Importance of Selecting Proper Material Handling Equipment
As you can tell, material handling has a huge impact on the productivity in your facility. Inefficient warehouses, distribution centers, and manufacturing plants are more prone to errors and delays, which will ultimately impact your revenue streams due to loss of customer loyalty and falling behind the competition. But there’s more to material handling equipment than improving the productivity of your facility. Every business should put in the time to assess and improve their systems in order to preserve the integrity of their products, the productivity of the facility, and the health of their employees.
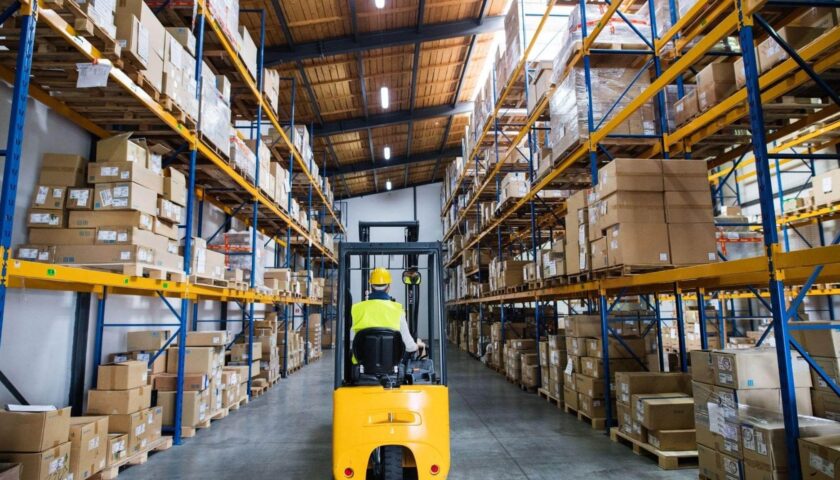
When you get a batch of materials or goods in your facility, your material handling process should ensure you get them from the unloading dock to the pallet rack (or any other type of storage system you have) in a timely and organized manner. In order to mitigate damage and spoilage, have select employees deal with the goods in that part of the process.
Improving Worker Morale
As aforementioned, there’s much more to material handling than just improving the productivity in your facility. Perhaps the biggest benefit of all is improving worker morale. A well-designed material handling system can allow employees to complete tasks faster and make the tasks less taxing. That being said, the material handling equipment you choose for your facility should be suited for your specific processes. For instance, if you operate a small warehouse with limited floor space, getting a trolley online rather than a forklift, even though the trolley is manual and the forklift is semi-automatic, may prove to be the more valuable option.

Improper material handling processes aren’t just risky for your employees’ physical health, but also their mental health. Activities deemed inefficient or useless can reduce the mental focus of workers, and unhappy workers are often unproductive. This can lead to increased turnaround rates and increased time off. As a result, you can get raised recruitment costs.
What to Pay Attention to When Setting Up Your Facility
Facility Layout
The ideal material handling system will largely depend on your facility layout. The layout can be the difference between an efficient and inefficient facility. A poor layout can result in bottlenecks, injuries that are a result of manual material handling, and increased motion waste. A well-designed facility, on the other hand, will streamline your processes, reduce worker movement and improve your workers’ physical and mental wellbeing.
Efficient Use of Space
Making the most out of your available space can go a long way in improving productivity. You need to take your storage needs into account, but also the needs of your workers. Do you have the available space for the needed restrooms and offices? Do you have a dedicated space to store your empty pallets, batteries, tools, etc.? By keeping your space, workplace flow and accessibility at the forefront, you can come up with an effective facility layout.
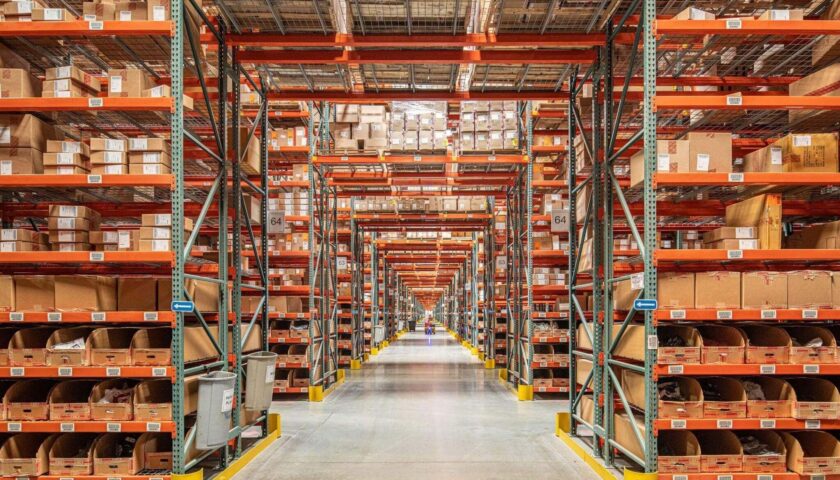
Determining Facility Objectives
Consider which processes you want to be prioritized in your facility. For instance, inventory management can provide greater benefits for your particular facility over material handling, or picking and packing can prove to be a more valuable process to focus on. Whatever the case, zero in on your goals, and structure your facility thoughtfully. But keep in mind that all processes are intertwined, and impact the efficiency of one another.
Types of Material Handling Equipment
After all this talk about material handling equipment, and just barely mentioning trolleys and forklifts, now is the time to go a bit more in-depth. Depending on your processes and goals, there are a few different types of material handling equipment that are generally separated into the following categories:
- Industrial Trucks – These are manually handled or powered vehicles used to move materials around. The most popular ones are forklifts, trolleys, side loaders and pallet jacks.
- Storage and Handling Equipment – This category generally includes pallet racks, shelving units and frames. Basically, everything that stores materials and products between the time they’re received and shipped.
- Engineered Systems – This category includes the automated units used to move goods throughout the facility and reducing the need for worker intervention. Some examples include robotic delivery systems, conveyors, automated storage and retrieval, automatic guided vehicles, etc.
- Bulk Material Handling – This is the equipment used to assist workers when handling bulk, or huge loads. Examples of this type of equipment include silos, stackers, bucket elevators, etc.
When all of these categories of material handling equipment are implemented in a way to complement each other, your facility’s efficiency will definitely improve drastically. For instance, conveyors can be used to move materials with a minimum amount of lifting required, and you can get overhead lifting equipment such as cranes and hoists to completely eliminate the need for manually lifting. Furthermore, this way, you can use your floor space for storage instead of maneuvering room for forklifts or trolleys.
Read Also: 5 Tips and Tricks for Managing a Manufacturing Business

-
Business3 years ago
How to Do Long-Distance Moves with Children
-
Travel2 years ago
Quick Guide: Moving To Santa Rosa?
-
Real Estate3 years ago
Why Dubai Festival City is a Great Neighbourhood for Young Learners
-
Business3 years ago
Is Guest Posting a Good Inbound Marketing Strategy?
-
Business1 year ago
The Ultimate Guide To Thriving In Your Printing Franchise
-
Business1 year ago
Exploring The Benefits And Challenges Of Restaurant Franchising
-
Tech3 years ago
Cyber Table That Will Change Your Life
-
Lifestyle1 year ago
Dallas’ Hidden Gems: 6 Must-Try Restaurants Off The Beaten Path!
Recent Comments