Business
Precise Movements With Linear Actuators In Robotic Engineering
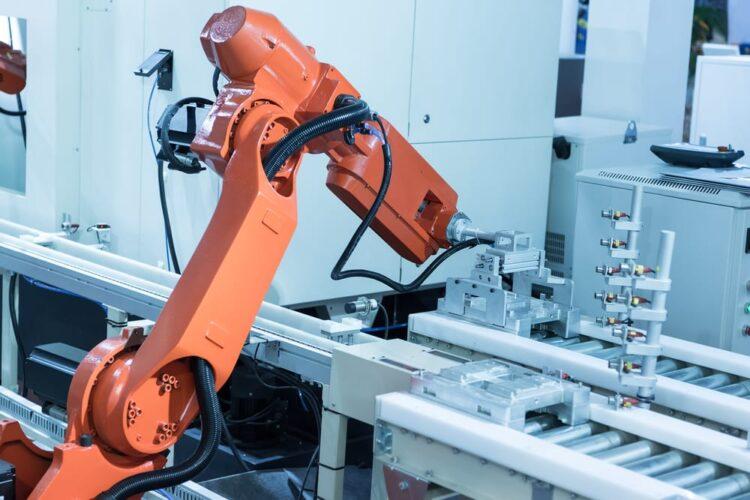
Table of Contents
Unlocking Precision: The Role Of Linear Actuators In Robotic Precision Engineering
Linear actuators and their multi-axis systems are crucial for the ever-changing world of industrial automation. These systems work really well for moving and positioning parts quickly and with a lot of care. Even though actuators are complicated machines, they make it much easier to produce dependable straight-line movements. Their precision ensures that tasks are performed accurately, enhancing overall efficiency.
Essential Elements That Affect Actuator Efficiency
Numerous important elements shape the performance of linear actuators. These elements include but are not limited to:
- The architecture and caliber of the internal components, such as gearboxes or lead screws, are crucial for ensuring the motion is smooth and the device’s operations are precise.
- The types of materials used for constructing guides and housings significantly affect the actuator’s longevity and the amount of friction it encounters.
- Feedback mechanisms, such as sensors and limit switches, are vital for precise positioning and enhancing system safety.
- The control of voltage and current within the power source dictates the speed of the actuator, the force it can exert, and how quickly it reacts.
- Environmental conditions play a substantial role too. Conditions like temperature, humidity, and the weight of the load the actuator must handle can greatly influence its effectiveness and durability.
Types Of Linear Actuators In Robotic Precision Engineering
Linear actuators come in various types, each suited for specific applications and offering unique advantages and disadvantages. Here’s a look at some common types:
Hydraulic Actuators
These are great for moving heavy loads because they can generate a lot of force. They work by filling a chamber with hydraulic fluid; when pressure is applied to this fluid, it pushes a piston, which in turn moves the output shaft.
Advantages: They’re straightforward to control, quite accurate, and provide a consistent force no matter how fast they’re moving, all while operating quietly.
Disadvantages: They can be messy to maintain, are more costly, and fluid leaks can harm the environment.
Pneumatic Actuators
These are similar to hydraulic actuators but use compressed air to move the piston instead of hydraulic fluid.
Advantages: They’re cleaner for the environment, less expensive, and simple to operate safely.
Disadvantages: They tend to be noisy, less precise, and are affected by vibration.
Electric Actuators
These are the most popular actuators in robotics. They turn electrical energy into linear motion and are typically used in DC form for robotic applications.
Advantages: They offer the best precision, are easy to connect and program, provide immediate feedback for troubleshooting, and allow full control over motion with encoders that manage velocity, position, and torque. They’re quieter and environmentally friendly since they don’t involve fluids.
Disadvantages: They have a higher upfront cost, though they tend to be cheaper to own in the long run.
Grasping How A Linear Actuator Functions
Linear actuators operate based on a variety of control methods that involve sending electronic signals. Although it’s not feasible to cover all possible methods in this discussion, let’s delve into some of the more prevalent ones used today.
DC Control
This method involves applying a direct current (DC) voltage to the motor via a switch, relay, or other controlling device. By changing the polarity of the voltage supplied to the actuator, you can reverse the direction in which it moves. This straightforward approach is fundamental yet effective for basic actuator operations.
Pulse Width Modulation (PWM)
PWM is a technique where a digital signal is turned on and off rapidly to create the effect of an analog signal. This type of control is pivotal in precision applications, as varying the length of the signal’s on-time versus its off-time (known as pulse width) allows detailed control over the actuator’s position. PWM is particularly common in systems using microcontrollers, making it a staple in embedded systems.
Programmable Logic Controllers
PLCs are advanced control systems widely used across various sectors, especially in industrial automation. They are capable of driving linear actuators using diverse signals, such as 4-20mA current loops. These controllers are valued for their versatility and reliability in managing complex operations.
Servo Control
Some linear actuators are designed to function as direct replacements for standard rotary servos, seamlessly integrating with systems that typically use these components. This form of control offers plug-and-play convenience and broad compatibility.
Moreover, many modern linear actuators incorporate feedback mechanisms like encoders or hall-effect sensors. These sensors provide crucial real-time data about the actuator’s position, enabling what is known as closed-loop control. This setup significantly enhances the accuracy and reliability of the actuator by allowing it to adjust based on its actual output, ensuring precise positioning and smoother motion control. This level of feedback is essential for applications requiring high precision and efficiency.
Linear Actuators: Enhancing Precision In Robotic Engineering
Linear actuators are crucial for the precise movements needed in robotics. They help robots handle intricate tasks by moving exactly right, every time. Also, because these actuators use sensors to make adjustments while they work, they keep robots accurate and reliable.

-
Business3 years ago
How to Do Long-Distance Moves with Children
-
Travel2 years ago
Quick Guide: Moving To Santa Rosa?
-
Real Estate3 years ago
Why Dubai Festival City is a Great Neighbourhood for Young Learners
-
Business3 years ago
Is Guest Posting a Good Inbound Marketing Strategy?
-
Business1 year ago
The Ultimate Guide To Thriving In Your Printing Franchise
-
Business1 year ago
Exploring The Benefits And Challenges Of Restaurant Franchising
-
Tech3 years ago
Cyber Table That Will Change Your Life
-
Lifestyle1 year ago
Dallas’ Hidden Gems: 6 Must-Try Restaurants Off The Beaten Path!
Recent Comments